Pipes
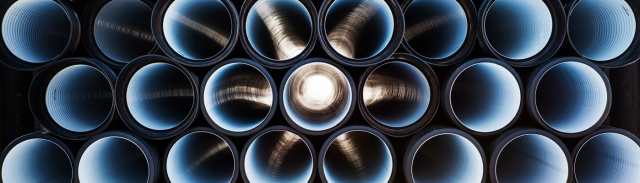
Polyethylene is a whole family of materials, often categorized in terms of density.
The application of PE in the pipe industry has resulted in a variety of materials being used which are low, medium, high density or even linear low density, abbreviated as LDPE, MDPE, HDPE, and LLDPE.
A performance-based classification and designation system was introduced in the mid 1990s for pipe, resulting in the publication of ISO 12162 (See Material Classification). A material is given a designation number based on the predicted long-term hydrostatic strength at 50 years and 20 °C, e.g. PE 80 or PE 100.
For pressure applications, the choice is usually between a PE 80 or PE 100 compound. PE 40 and lower class LDPE materials have diminished in use for pressure pipe but are used for small diameter irrigation applications. The first generation HDPE materials would fall into the PE 50 or PE 63 class, but would only be used for non pressure or ducting applications nowadays. These have been long superseded by superior performance second generation PE 80 and third generation PE 100 materials.
There is a choice of PE 80 compounds which can create some confusion. There are unimodal HDPE and MDPE materials meeting the PE 80 classification. However, generally such HDPE material types can barely meet the requirements of current PE pipe product specifications, and are being phased out by most suppliers.
The unimodal MDPE PE 80 materials offer excellent performance, but might be considered second choice to PE 100 nowadays and limited to service pipe. Some gas companies prefer to continue using these materials for their low pressure systems for historical reasons and because of the pipe's installation flexibility. Following development of the bimodal PE 100 materials, not surprisingly most suppliers have used the same process to produce bimodal PE 80 materials. Although these offer notably improved RCP resistance over unimodal PE 80 materials, such materials have not really found their place in the market. PE 100 materials are the economic choice for large diameter pipes and the performance of unimodal MDPE PE 80 materials is adequate for smaller diameter service pipes.
Clearly, PE 100 has the advantage of a higher design stress allowing operation at higher pressures or even wall thinning, and the products have greater fracture resistance for large diameter pipe. PE 80 MDPE has more flexibility for ease of installation but this is not a significant advantage. PE 100 materials are suitable for all applications, even including service pipes provided the extra stiffness is taken into account when handling coils during installation.